Treatments
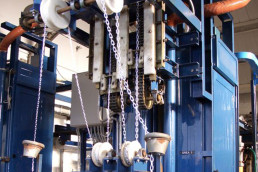
BLUCROM ELECTROLYTIC GALVANIZING PLANT
(UNI ISO 4520 e UNI ISO 2081)
One of our studies has allowed us to develop the new BLUCROM galvanizing system, perfectly compliant with the European Directive nr. 2200/95/EC (RoHS), regulation which, among the various directives and obligations on disposal, prohibits the use of hexavalent chromium.
The plant has the following specific characteristics and prerogatives:
- The in-line galvanizing process allows an innovative chain self-tensioning system, and guarantees a uniform zinc deposit even at the junction points of the links.
- The constant thickness of the deposit determines the best possible protection of each single link, coating the chain deeply and homogeneously.
- The BLUCROM galvanizing ensures a high resistance to atmospheric agents providing the chain, at the same time, with the characteristic and unique bright BLUE colour.
HOT GALVANIZING PLANT
(EN ISO 1461 STANDARD)
Hot-dip galvanizing takes place by immersing the chains in molten zinc held on average at a temperature of 455°C, covering them entirely. Thanks to the pre-treatment in a bath of molten salts of zinc chloride and ammonium chloride, the steel of the chains binds to the zinc giving higher corrosion resistance than in electrolytic zinc plating, also due to the greater mechanical resistance of the protective layer.
The process can be divided into the following stages:
- Pickling and degreasing: obtained with hydrochloric acid and surface-active agents at ambient temperature;
- Flushing: immersion, in ammonium chloride and zinc chloride solutions;
- Galvanizing: immersion, after preheating at 100°C, in a tank of molten zinc at 455°C for the time required for the chains to reach the same temperature as the zinc.
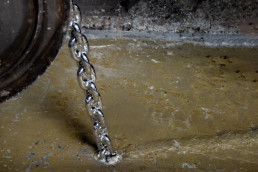
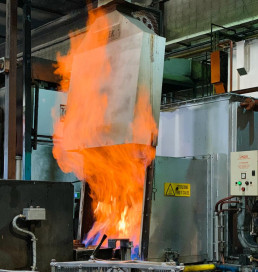
HOT TREATMENT
(carbunization + hardening)
All our safety chains are subjected to HT treatment (carbunization + hardening)
HT is a thermochemical diffusion treatment which provides an enrichment of carbon on the surface of the chain. This treatment is carried out in a controlled atmosphere at a temperature that generally varies from 870°C to 940°C. Carburizing is normally followed by a hardening treatment in oil and subsequent tempering to obtain the required surface hardness.